volara®
volara® - Compliant Measurement Processes
volara® is a cloud-based platform and supports users in implementing of test process management completely in accordance with VDA Volume 5.
Measuring devices can be selected from an in-house, customer-specific or public test equipment database. volara® can be integrated into the customer’s IT infrastructure.
volara® establishes not only the capability of measurement and test processes, but also consistency with the adjacent processes of test equipment management and test planning. The integrated risk-based approach provides support in selecting the procedure for validating test decisions and allows differentiated methods.
Test process management, capability analysis, test equipment database and/or test planning
Depending on the requirements and initial situation, volara® enables the various entry points for the management of measurement and test processes, the approach for planning and for the implementation of capability analyses. This depends on the respective use case:
- What data (studies) are already available?
- How detailed should the study be planned?
- Should a risk assessment be carried out?
- Is the integration of a test equipment database possible or desired?
- Do you first start with a test plan or
- do you go through all stages of the process right up to comprehensive reporting?
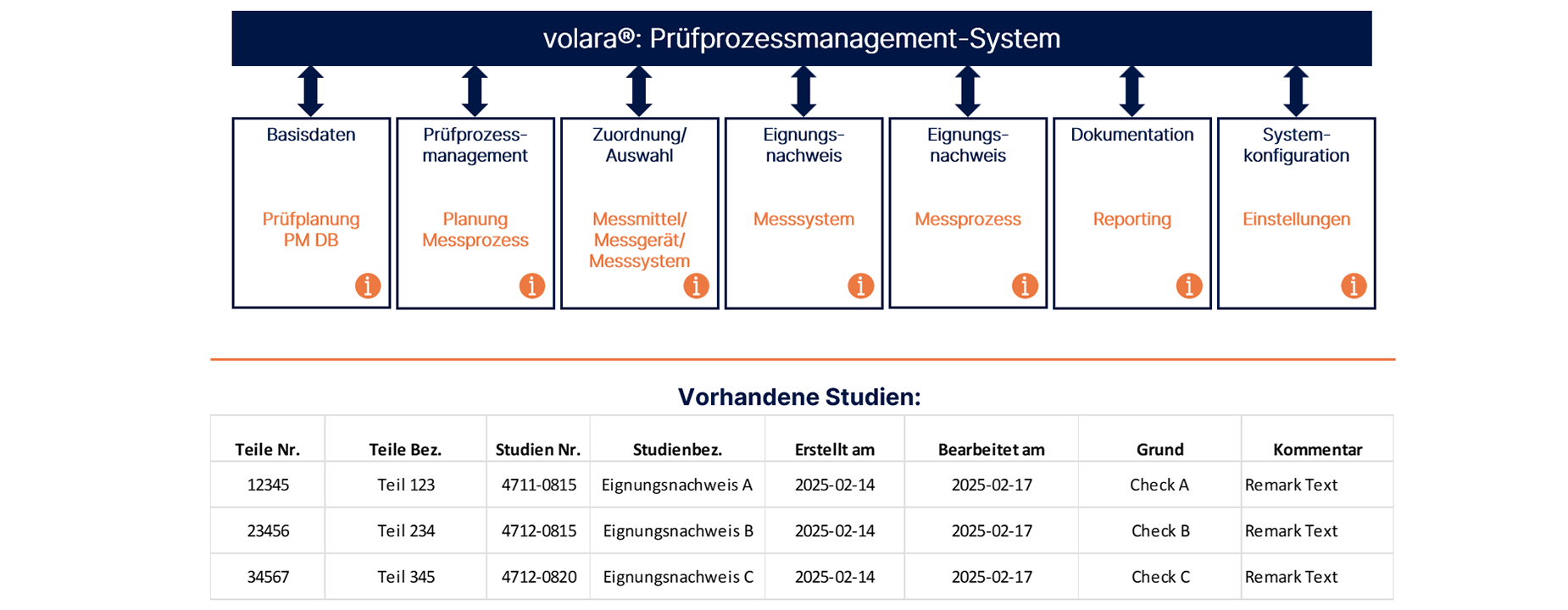
There are separately bundled function blocks for each entry point (inspection planning, test process planning, selection of measurement equipment, measuring system capability, measurement process capability and reporting) to guide you through the respective tasks in a targeted manner. The entry points relate to each other, but do not necessarily have to be completed in full.
Some functions and information can be found in various entry points. They do not have to be entered again during subsequent processing, but volara® automatically takes them from data that has already been entered, imported or assigned. This means that a later completion of the other entry points is already filled with data from other use cases.
volara® offers quick access to studies that have been started or completed in the start menu in order to process them further or view the results. Filter and sorting criteria support the quick selection and loading of existing studies.
The “Info” icon can be found in many places in volara®. This can be used to display additional descriptive information/documents, explanations of the standard uncertainties (in the measurement uncertainty budget) or recommendations and reference points.
Workspace and navigation in volara®
Selecting one of the entry points takes the user directly to the work area of the respective use case.
volara® guides the user through the input masks and function areas with the help of an intuitive structure. The header contains the main menu items (use cases), which can be switched between at any time. The status bar on the left-hand side shows which step the user is currently in. The respective status can be recognized by the circle:
- Filled circle = data recorded
- Empty circle = no data available yet
The status bar is also used for navigation and switches the central work area. If there are several product characteristics in a study, a feature list can be displayed to navigate between them.
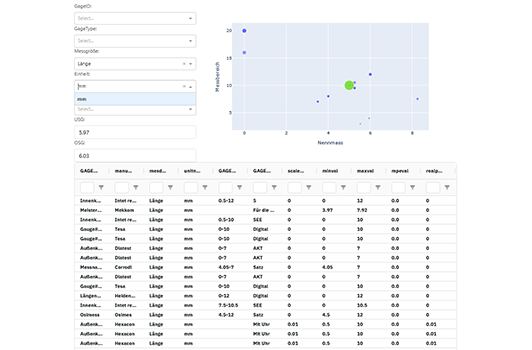

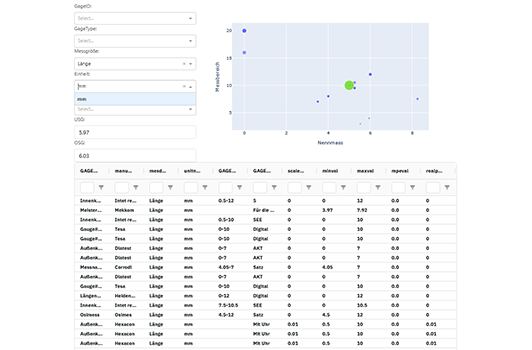
Test planning and PM DB
The basis for every study in volara® is the test plan, i.e. the specification for the part type and characteristic information. The test plan is the starting point and essential data carrier for the creation and processing of a study.
volara® offers various options for this. If no test plan data is available in a common format, the test plan can be generated manually. By entering the planning data (part type, number of characteristics, …), the corresponding input matrix is created. volara works on a database basis and defined header data from part type and study information represent the unique key for tracking studies in the system.
In many cases, however, data for inspection planning is already available in common file formats (csv, dfq, txt, …), so that a large part of the data input has already been carried out using import functions. If CAD drawings are available, these can also be imported into volara® and the product characteristics can be identified from the drawing using integrated AI algorithms.
The proposed mapping of the part type and characteristic information can be customized in a preview window before it is transferred to volara®.
The connection of a test equipment database is one of the central and essential elements of the software. volara® has its own test equipment database in which measuring devices, measuring equipment and measuring systems can be stored. It is a continuously growing knowledge repository. However, volara® can also be linked to the customer’s existing test equipment databases. This means that a large selection of stored measuring devices, measuring equipment and measuring systems is already available for test process management.
Another option for connecting a test equipment database is the “Public PM DB”. volara® has the option of directly accessing specifications and stored statistics of measuring devices. With an intelligent suggestion system, volara® screens the Public PM DB and suggests suitable measuring devices, measuring equipment or measuring systems for planning the test process.
Planning the measurement process
The planning of the measurement process requires interdisciplinary cooperation with team members from all responsible or necessary areas in the company. Specific knowledge (function of the component, properties of the production process, environmental conditions, planned measurement concept, …) must be available in the team. Planning the measurement process is an essential part of test process management.
The information is queried and stored in topic-specific areas in volara®. Accompanying additional documents (e.g. for the measurement concept, etc.) can be stored.
Based on the description, the measurement process is analyzed with regard to the expected influences. The analysis is carried out using the Ishikawa diagram, in which the important and relevant influencing parameters are recorded and evaluated. The categories and causes can be freely defined, structured and visualized.
Determining the risk class
Risk-based assurance is the estimation of the risk that would result from an incorrect test decision. According to VDA Volume 5, a distinction is made between three cases: Case 1: highest risk; Case 2: no risk and Case 3: all other risk areas. The result of a risk assessment is the decision as to whether or not a capability analysis is to be carried out (subject to documentation!).
In volara® , catalog-based criteria can be defined that describe the severity of a defect and its probability of occurrence in the categories “high”, “medium” and “low” (criteria in the graphic are examples from VDA Volume 5).

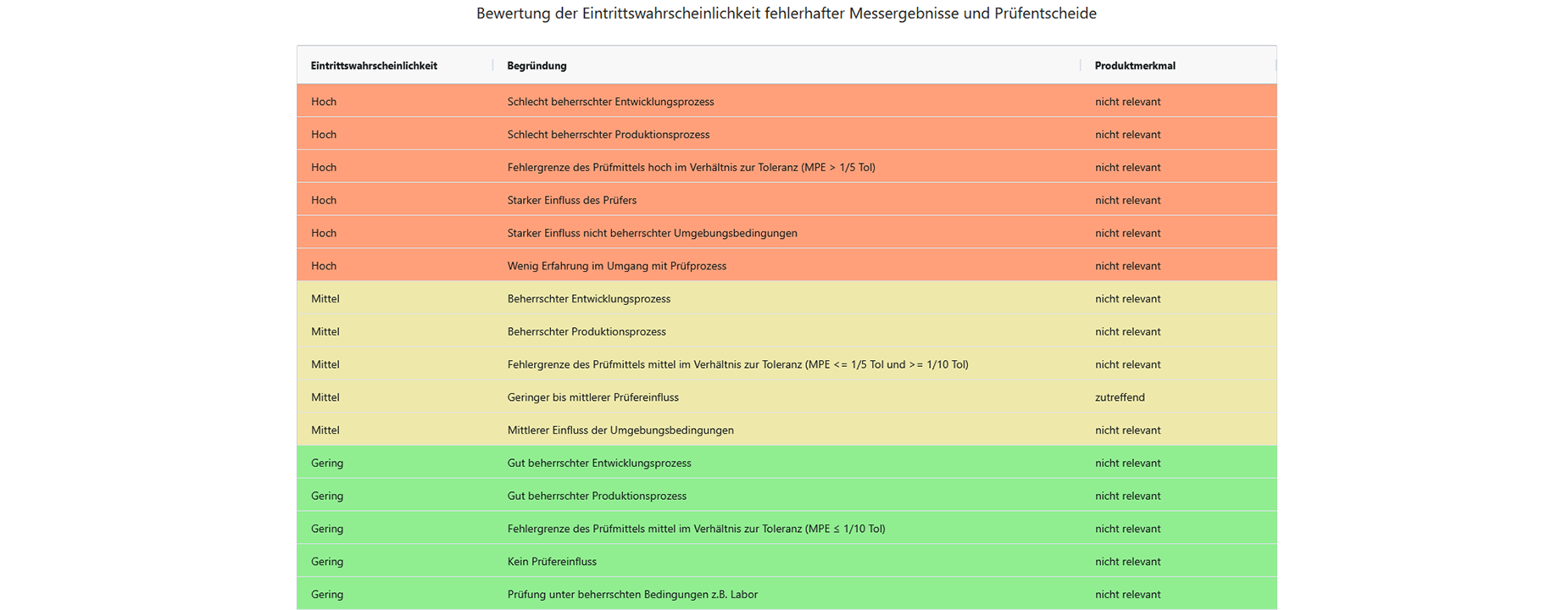

Selection of measuring system
As described under “Test planning and PM DB”, the connection of a test equipment database is an essential component of volara® and a clear added value for the user. volara® has different options for the connection: volara® own test equipment DB, customer-specific test equipment DB or a public PM DB.
A suitable measuring device, measuring equipment or measuring system should/can be selected as early as the test planning stage if the relevant information is available. Based on the characteristic information (characteristic type, resolution, specification limits, …), volara® searches the database for a suitable measuring device, measuring equipment or measuring system and suggests this to the user for the respective measuring task.
Here, volara® takes a multi-stage approach for a specified feature:
- If uMS values are available for the characteristic based on existing studies (type-1 or evaluation of linearity), the measuring systems that qualify with regard to the QMS value are proposed.
- If measuring devices or measuring equipment are suitable for the characteristic and the MPE value (Maximum Permissible Error) is stored for them, the combined measurement uncertainty uMS value is determined from this, taking into account the distribution, and all measuring devices or measuring equipment that qualify with regard to the QMS value(≤ 15%) are suggested.
- If no uMS value is known, volara suggests all measuring devices or measuring equipment for the characteristic that have a resolution of %RE ≤ 5%.
In addition to an intelligent suggestion system for the selection of measuring instruments from the database for the further preparation of a capability analysis, study results such as the combined standard uncertainty uMS can also be saved back into the test equipment database after a capability analysis has been carried out. Thus, with every study carried out in volara®, the qualified knowledge grows continuously and provides important decision criteria for the subsequent or new selection of measuring devices, measuring equipment and measuring systems.
This offers the user an enormous advantage, as the study results for the measuring device, measuring equipment or measuring system are not only provided as a decision-making aid, but are also loaded. This means that the data is already availableto establish the capability of the measuring system in order to be able to create the uncertainty budget for the measuring system.
Capability of measuring system and measurement process
The central element in volara® is the measurement uncertainty budget. It summarizes the determined standard uncertainties assuming an additive measurement model to illustrate the capability of the measuring system and measurement process. Standard uncertainties that contribute the main amount to the measurement uncertainty can be quickly identified via the ranking and identified for possible optimizations or conclusions. Additional information and the relevant capability indices are displayed for each standard uncertainty.
volara® offers a preselection of measurement process models and the associated standard uncertainties. These refer to the definitions in VDA Volume 5 in order to simplify the procedure. In addition to a selection of the stored measurement process models, an individual selection of the standard uncertainties for capability analyses is also possible.
In many cases, measurement data for the measuring system (type-1, linearity study) or the measurement process (type-2, type-3) is already available and can be imported in standard formats (csv, dfq, txt, …). This step is particularly suitable if you want to achieve a quick result of a process capability analysis based on existing data. Subsequent input of basic, planning and preparation data is possible at any time. The measurement data can already be displayed in characteristic graphics during import. The data sources are selected in a user-guided dialog and any necessary modifications to the header data can still be made. A graphical preview of the selected data for the import shows the selected measurement data. volara®’s central element is the measurement uncertainty budget. It summarizes the determined standard uncertainties assuming an additive measurement model to represent the suitability of the measuring system and measurement process. Standard uncertainties that contribute the main amount to the measurement uncertainty can be quickly identified via the ranking and identified for possible optimizations or conclusions. Additional information and the relevant capability indices are displayed for each standard uncertainty.
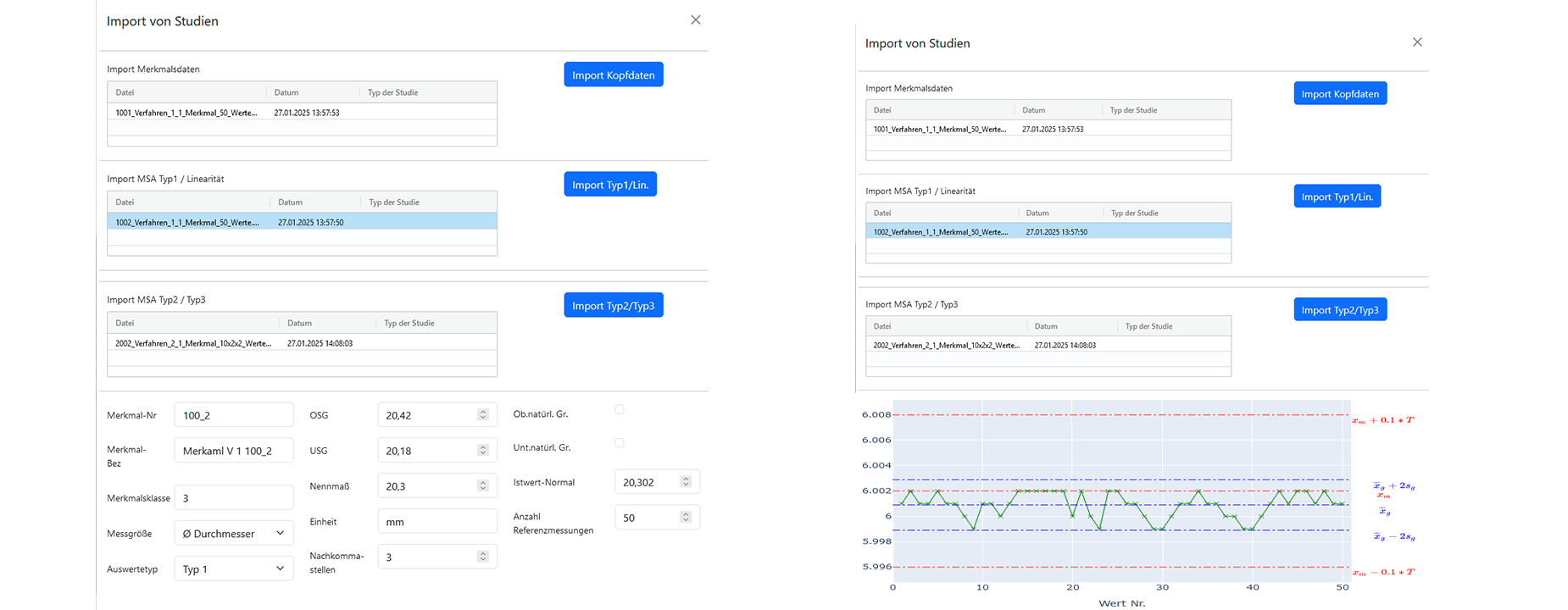
If the import only contains header data and no measurement data, these can be added in volara. In order to be able to do this, the planned type of recording must be defined (selection of the method and the necessary recording criteria in order to build up the matrix). An import (copy-paste) is also possible via the clipboard.
The measurement uncertainty budget is not only a result display in volara®, but also serves to assist the user (receiving explanatory information and graphics), adding accompanying documents (e.g. calibration certificate), accessing the test equipment database and also interactively modifying the measurement uncertainty budget. Standard uncertainties can be subsequently added, deselected or changed in order to investigate influences on the uMS measuring system and/or the uMP measurement process, or new data records can be loaded or entered
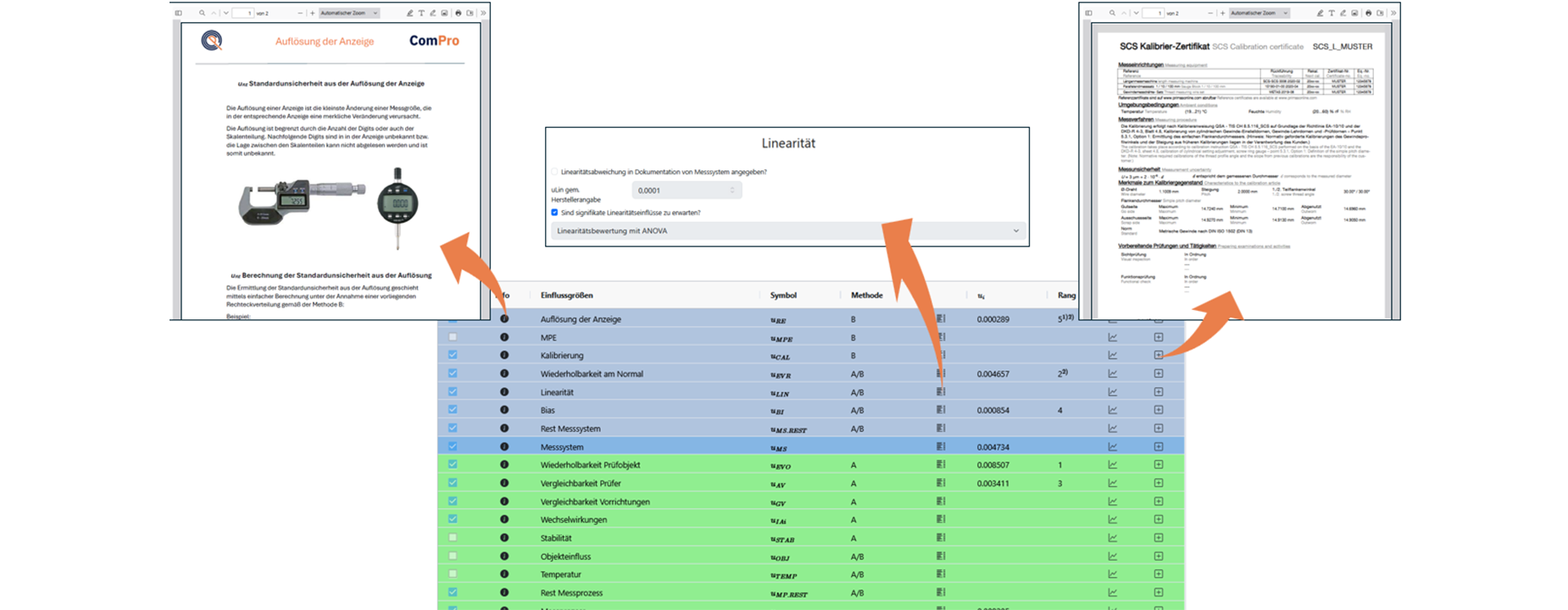
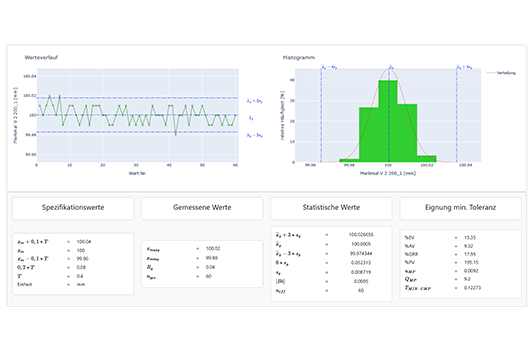
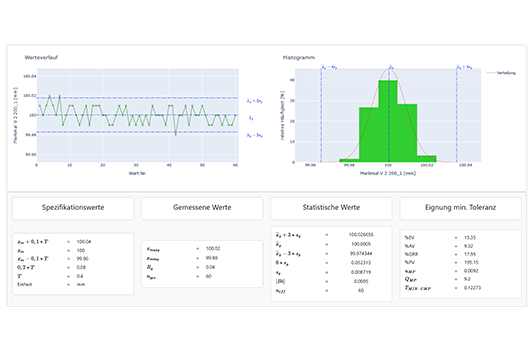
The analysis results in volara® not only document the capability of the measurement and test processes (QMS and QMP as well as TMIN-UMS and TMIN-UMP) in accordance with VDA Volume 5, but the available data from the MSA studies can also be used to display corresponding reports.
Reporting overview
There is a summary report for each use case. This can be accessed in the respective status bar and documents the recorded data and results. Reports document the contents and results of volara®. However, they can also contain additional documents (e.g. calibration certificate, measurement concept, etc.). The reports are based on templates provided and are filled with data record-specific information. Individual templates can be created at any time.
An overview of all reports can then be found in the “Documentation/Reports” area.
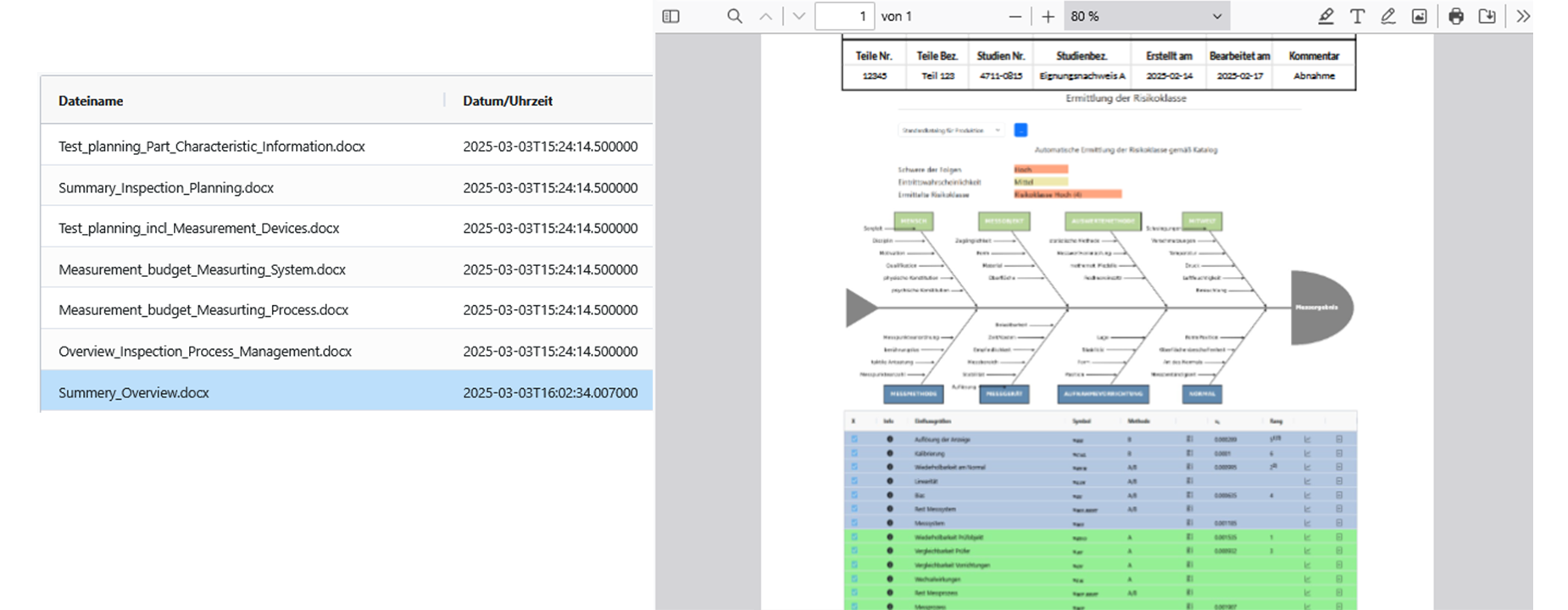
Get in touch with us!
Do you have any questions about volara®, our training offer or would you like to request an individual offer?
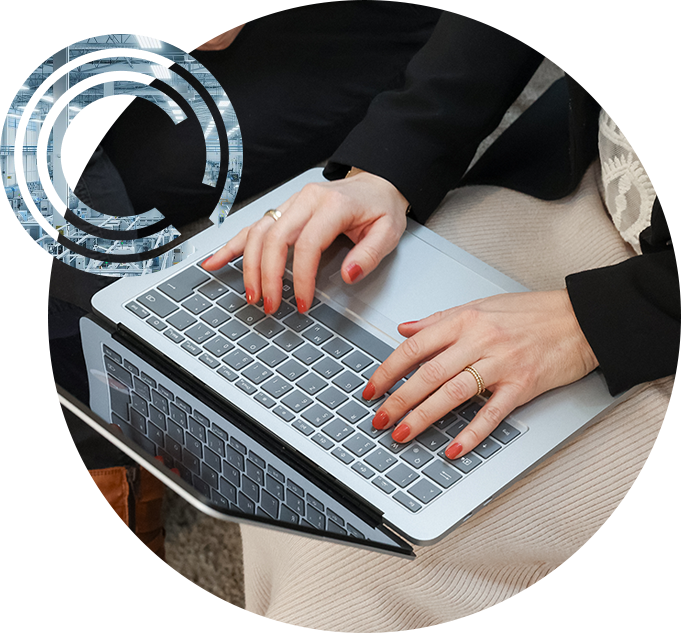